Wednesday Writeup: Integrated Testing
- Sarah Whiteford
- Mar 19, 2020
- 2 min read
In February, news regarding the investigation into the Boeing Starliner's failure to reach the ISS was released. The article pointed to specific integrated testing protocols which had not been completed as part of the preparations for the launch. It also pointed out the other arm of the aerospace giant currently suffering from software/hardware integration issues: the 737 Max.
Boeing certainly isn't alone in having a disconnect between the system testing protocols of the last 30 years and the complexity of their new systems. In fact, we are regularly identifying where our traditional methods fail us in the new age of complex systems; from self-driving cars and manufacturing to offshore infrastructure.
The key part of any integrated system assessment process, from Hazard Identification (HAZID), Hazard & Operability (HAZOP), Failure Modes Effect Analysis (FMEA), or System-Theoretic Process Analysis (STPA) is to identify, mitigate and validate your assessment.
How do we validate the increasingly complex systems we are developing? Enter the concept of integrated testing.
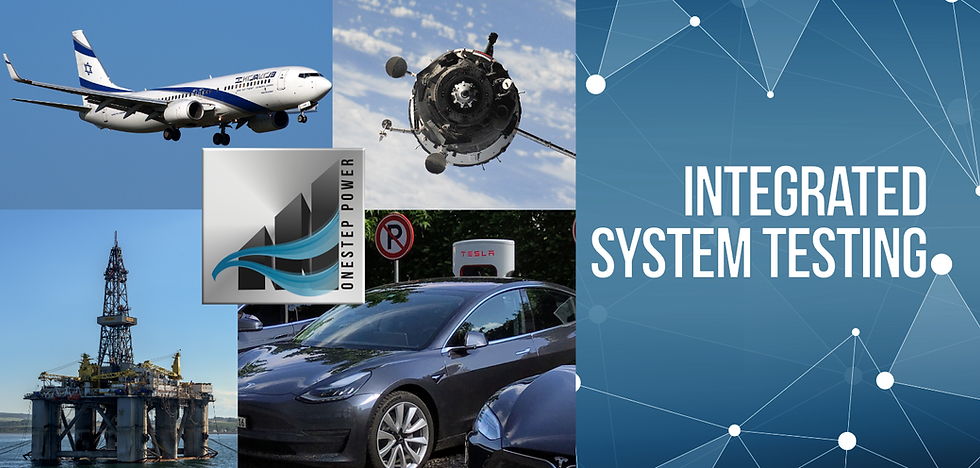
Integrated testing takes a number of forms. In an ideal (new-build) world:
Each component is tested at the factory as part of Factory Acceptance Testing (FAT).
Integrated control systems are tested against one another in a Hardware in the Loop (HIL) environment
The discrete components are assembled in a shipyard/fabrication yard
A System Integration Test (SIT) or Sea Trials is performed as applicable to test the operation of the full system.
In the case of a Dynamically Positioned Vessel, an FMEA Trials program is performed to prove the failure cases of the vessel comply with worst-case failure design intent.
What happens when we add risk factors after the initial assessment?
In offshore oil and gas, the battery hybridization and alternative fuels discussion is primarily aimed at retrofitting existing vessels. How deep can these projects go in their investigation of the changes to the integrated system as a result of the retrofit? Time and money play a significant role in the decision-making, while everyone still wants assurance of a safe solution.
It's not enough to simply confirm the operation of the hybrid system and the new safety features. The integration of new systems needs to be validated in conjunction with the existing system.
Some Examples:
Has the new fire fighting equipment been integrated into the onboard fire control system? Has the logic change been regression tested and a full operation check of the system been completed? (I'd ask if the fire mains have been tested, but if you have water-based fire suppression systems in your battery rooms you have another issue entirely.)
Has the battery status system integration with the control room interface been regression tested and the logic confirmed to not interfere with normal operation?
Has the system's power failure modes been checked against the battery installation?

Has the system's changed behavior in the event of a fault been confirmed? Include short circuits on propulsion drives, inverter short circuits, load steps, system imbalances, engine-room shutdowns, and numerous other failures.
Has a network storm test been completed on the systems affected by the upgrade?
This process rapidly becomes almost as complex as the system you just installed!
OneStep Power can help you take some of the guesswork out of integrated battery-on-board testing. Contact us, we'd love to help!
#wednesdaywriteup #powertesting #faultridethrough #voltagedip #integratedsystems #integratedtesting #offshore #offshorelife #STPA #FMEA #EnergyTransition #innovation #TechnologyAdoption #Marine #Batteryonboard #hybridpower #hybridvessel #Maritime #Eferry #Ecruising #dynamicpositioning #DPFMEA #OneStep
Comments