How do jack-ups work?
- Sarah Whiteford
- Mar 19, 2021
- 5 min read
It’s Fun Fact Friday and we’re going to take a look at jack-ups. These rigs use retractable legs to stand above the waterline and perform underwater work, acting as a floating barge that turns into a stable platform above the waves. Why is such a large platform needed? To answer that, let's take a look at where oil and gas retrieval begins, upstream.
Oil and gas starts with upstream activities, where natural resources are extracted from the Earth. With permission from governments, oil companies start exploring for oil and gas deposits with geological, magnetic, gravity, and seismic surveys. When a promising location is found, an underwater tower called a jacket is installed on the sea bed. The jacket will help guide the drill pipe for drilling, and if oil is found, a top side will be installed on the jacket to hold construction facilities. A drill crew is then brought in to drill the well, which can take somewhere between a few days to months to complete. When oil and gas are found, the well is capped with a well head, and construction begins on a production facility to produce oil and gas.
Where does the jack-up come in?
Jack-up drilling rigs are mobile offshore drilling units, or MODUs, pronounced "moe-dooz". Semi-submersibles and drillships handle deep water drilling of up to 12,000 feet of water, but MODUs excel in shallow and coastal areas of 400 feet or less. Instead of floating above the well for drilling, they are what is referred to as bottom supported units, in other words they rest on the sea bed. Most wells are drilled by jack-ups, although new wells are being found in deep water, as most coastal areas have been heavily explored.
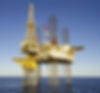
Ensco-56 Jack-up. Image credit: RigZone.
Because these rigs are mobile, they generate their own power and water, and house the crew for long periods of time. Jack-ups typically have three or four legs that are extended down to the sea floor. The drill is either cantilevered over the side of the vessel or mounted to be used through a slot in the hull. Jacking up the rig on the ocean floor creates a stable platform above the waves on which it is easier to work. All of this is to support the drilling process, so the rigs have to be ready to relocate when drilling has finished. When it’s time to move, rigs retract the legs up, which can make them somewhat unstable. Once up, there are three options for movement. If the distance the rig needs to travel is long, the rigs stay up high and a heavy lift ship floats underneath the rig, filling its ballast tanks to stay low in the water. Once in position it can empty the tanks and the rig can be lowered down onto the ship and transported. For shorter journeys, rigs can also be towed into place, many times after being transported on a ship for the longer leg of a journey. Rigs are basically floating barges, and are subject to the same standards as other ocean-going vessels, and governed by the same classification societies like DNV and ABS.

“Shelf Drilling’s new-build “Krathong” being carried on a heavy lift ship.” Image credit: Benjamin Charlton at Templato blog.
What about the legs?
Legs of a jack-up are a strong lattice structure. The verticals on the outside of the structure are called chords, which can be triangular, in groups of three, or a square cross-section with four. Jacking motors use a rack and pinion system with notches on the chord where the gears mesh to raise and lower the vessel. Legs can also be columnar, but this type of leg is not as strong as open truss legs, so they are only used on vessels that operate in less than 250 foot water depths. The legs actually sink into the ground, and usually contain jetting lines that agitate the sea bed to help the legs sink deeper, as well as loosen the legs when it’s time to move. The bottom of the leg is called a spud can, and this acts as a cleat to dig in and keep the rig in place. Jack-ups also have ballast tanks, which can be filled with water to pre-load the legs and drive them down for solid footing. It also ensures that there isn’t a false bottom where a rig leg could fall through and be damaged.

Drawing of a jack-up drilling set up. Image credit: Benjamin Charlton at Templato blog.
Drilling technology
The cantilever system that holds the drill over the side of the vessel can be moved horizontally and vertically, even drilling multiple wells mere feet apart. Drilling rigs also contain drill pipe, with multiple pieces installed end to end. These pipes can be thousands of feet down below the surface, and flexible enough to curve in different directions. They are capped with a drill bit that grinds away rock, sand, or other material. There is also a casing layer, a pipe made of concrete that supports the bit and is extended as the drilling goes deeper.
What about safety?
Wells are equipped with a blowout preventer, or BOP that contains pressure from blasting up the well uncontrollably. They can close the pipe or divert pressure for safety. There is extensive other safety equipment - according to Benjamin Charlton, “The rig is vulnerable to pretty much every natural and man-made hazard you can think of; hurricanes, fires, explosions, flooding, gas leaks, pirates, helicopter crashes, punch-through, BOP blow-outs and collisions with other ocean-going vessels.” Safety systems include “watertight doors, spill clean-up kits, lifeboats, liferafts, life-jackets, fire and gas alarms/detectors, portable fire extinguishers and sprinkler systems.” Additionally, everyone on a rig is trained for safety and there is ample room in lifeboats for everyone on board.
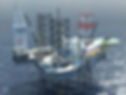
Cantilever drilling skid on a jack-up drilling rig. Image credit: Benjamin Charlton at Templato blog.
What about WTIVs?
WTIVs, or Wind Turbine Installation Vessels, are vessels specifically designed to build wind farms. Many of these are jack-ups that operate offshore in shallow waters where winds are stronger and more steady, and turbines can’t be seen from shore. In 2010, the second generation of jack-ups for wind turbines were created, followed by the third generation jack-ups that were started in 2015. Each generation hoped for a 25-year lifespan, but turbines continued to grow significantly in a short amount of time, with 8 MW turbines now being replaced by 14 MW turbines. A new fourth generation has been created, with vessels like the Voltaire and the Neptune handling the biggest jobs. These vessels are very large, capable of installing the current largest 14 MW turbines and larger sizes still in development. They need to move quickly around wind farms and are self-propelled with azimuth thrusters and dynamic positioning systems, like the DP2 system on the Neptune. To maximize efficiency and minimize trips to shore, they have the ability to carry multiple turbines. Usually on four legs, they have a massive crane to install blades over 100 meters in length on turbines 260 meters tall. This new category of jack-ups are much different from drillships and will see a lot of work as more wind power moves farther offshore.

WTIV installing a future 15MW wind turbine. Image credit: Offshore & Marine Technology.
Jack-ups are unique vessels that operate in shallow waters for construction like drilling, dredging, and wind turbine installations. They float, stand on the bottom of the seafloor, and can be either towed to a new location or self-propelled in the case of WTIVs. These marvels of engineering can cost half a billion dollars and take significant time to design and build. If you’d like to see an example video of how jack-ups work and how a wind turbine is installed by a jack-up, check out the video below.
Happy Friday!
Sources: