How do cable lay vessels work?
- Sarah Whiteford
- Mar 6, 2021
- 4 min read
It’s Fun Fact Friday and today we’re going to take a closer look at cable lay vessels, why they’re needed, and how they operate. So, why do we need cable lay vessels? Over a million kilometers of submarine data cable runs along the ocean floor, connecting people around the world. Satellites can’t handle the flow of data required, so these fiber optic cables transmit voices, audio, and images all over the globe. You can find out more about how these cables work in our article “How do undersea data cables work?”. But, these aren’t the only type of cable these vessels work on; there is a growing need for electrical cable. The rapid expansion of offshore wind power has increased the need for electrical cable, which must be run between each turbine and to shore. These wind farms are being built farther and farther out, so miles of cable are now necessary for these deep sea installations. First, let’s dive into what makes these cable lay ships unique, and what they do when they’re not laying cable.
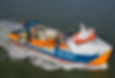
Cable lay vessel Nexus. Image Credit Van Oord, Offshore Fleet.
Cable ship names are commonly preceded by “C.S.” for cable ship, but even if they aren’t you’ll probably know a cable laying ship when you see one. There are two characteristics that make them immediately identifiable: the stern sheaves and the large carousels or baskets that hold the cable. The stern sheaves are designed to make cable laying easier, which used to be done from the aft, but in modern vessels is usually done from the stern, or rear. The carousel is a huge basket where the cable is stored, usually near the middle of the ship. Large ships may have multiple carousels that each hold thousands of tons, or up to 3,000 kilometers of cable in total. This much cable means cable lay vessels commonly sit at port for weeks loading cable into the carousels. If the manufacturing facility is near the harbor, cable can even be loaded onto a vessel as it’s put together. During shift changes the cables are tested to ensure the loading process has not caused any damage. When not installing cable, these ships can also service and repair existing cable, although this job may be done by smaller cable repair vessels that are smaller and more maneuverable. The newest ships are built for the dual purpose of laying and repairing cable, like the USNS Zeus that can lay 1000 miles of cable at 9000 feet depth.

Cable loading into a carousel. Image Credit: Van Oord.
After the cable is loaded into the carousels and the ship starts the installation process, the cable is fed out of the baskets into a plough. The plough is the device that digs into the ocean floor, creating a trench in which the cable is buried. These ploughs can be used for transatlantic cable, inter-array wind farm cabling, and export cable burial. The Sea Stallion plough below is a Royal IHC design that has been used for over 20 years of cable burying. The route taken by the vessel is pre-planned and very specific to avoid coral reefs, underwater rocks, and areas that are commonly used to anchor ships or fish. In some areas, cable can be left on the ocean floor, where it is occasionally attacked by sharks, as you can see from the video on Mental Floss.

Royal IHC Sea Stallion cable plough. Image Credit: Royal IHC.
Since cable laying is a very precise job done in an imprecise environment, cable lay vessels have dynamic positioning systems. These systems use computer control to keep ships exactly where they need to be, even in high waves or inclement weather. These systems are also necessary for repair work as the ship will likely need to stay in one place while a Remotely Operated Vehicle (ROV) or diver goes underwater for the service. Dynamic positioning systems are rated as DP1, DP2, or DP3, for different levels of redundancy. DP1 vessels are the most basic level, while DP2 have additional redundancy built into computers, power systems, etc, and DP3 systems have the most robust systems. Cable lay vessels are generally DP2 or sometimes DP3 due to the nature of the jobs they undertake. DP3 is also required if there are divers involved, so cable repair vessels need level 3 redundant systems for safety. The failure of a DP system could damage equipment, break cables, or leave a diver underwater as it did in the true movie Last Breath.
Cable laying technology continues to be developed as more and more cables are being laid for transmission of ever increasing amounts of data. Prysmian Group is about to launch a new vessel in Q2 2021 that will support the growing submarine cable market projected to hit USD 26.16 billion by 2025. Leonardo da Vinci is an advanced cable laying vessel that can travel over 14 knots maximum speed and carry a total of 17,000 tons between two carousels, the highest capacity of any cable lay ship. The €170 million vessel is equipped with a DP3 system for challenging installs. It can stay operational for 90 days autonomously, powered by a hybrid system, and will contain two underwater ROVs.

Leonardo da Vinci. Image Credit: Prysmian Group.
For more on cable laying vessels, check out this video from Boskalis.
Sources: