Additive Manufacturing – what is it?
- Sarah Whiteford
- Mar 18, 2022
- 8 min read
Before CAD, before 3D printing
Before there was any 3D printing or computer-aided design (CAD), making a prototype or model was a difficult process. Designs were carved from wood, glued together with plastic, or as is still done sometimes today with automotive designs, sculpted with clay. Changes to a design were costly and could involve the creation of an entirely new model by hand. If this was outsourced, there were additional costs with transporting items and communicating changes. In the 1980s, the idea of rapid prototyping (RP) began: create prototypes with automated equipment and cut the time down from weeks to days or hours. This results in a better product due to the ability to make multiple models and change designs quickly, as well as a reduced cost. More recently, 3D printing, or additive manufacturing has taken the spotlight as a way to create not only plastic models, but parts made from materials like metal that are ready for service and don’t require expensive molds or machining. The term rapid prototyping isn’t used as much anymore, since 3D printed parts are no longer just for prototypes and are being widely used in real-world applications.
Video on additive manufacturing from Additive Manufacturing Media’s YouTube channel.
How does 3D printing work?
The 3D printers most people are familiar with work just like a traditional paper printer, except instead of printing a microscopic layer of ink, they print a layer of plastic over and over again to build an object from scratch. This is the opposite of machining or carving, where material is removed until what is left is the final product. According to Explain That Stuff: “A 3D printer essentially works by extruding molten plastic through a tiny nozzle that it moves around precisely under computer control. It prints one layer, waits for it to dry, and then prints the next layer on top.” This can be anything ranging in quality from an extremely detailed part with smooth edges and complex shapes to a rough shape with plastic lines visible to the naked eye. Quality depends on what you need for the end product, the type of plastic used for printing, and the quality or resolution of the printer. Commonly used materials are ABS, which is the same material as LEGO® bricks and has a 220 F melting point; PLA which is a little softer; and PETG, which is between the two. If plastic isn’t your thing, then there are even food printers available – you can even print your own chocolate! We have to mention medical applications as well, as there are companies working on printing organs and bones.

Close up of a 3D printer. Image from Medium.
Additive Manufacturing vs 3D Printing
Additive manufacturing is the term for manufacturing objects by the addition of material rather than the subtracting of material like milling or the forming of material through stamping or pressing. The term 3D printing is usually associated with plastics and hobbyists while additive manufacturing is used for industrial and commercial applications, according to Hubs. The first commercial 3D printer was released in 1987 by 3D Systems, called the SLA-1, followed in 1992 by FDM and SLS printers, and finally in 1994, the first commercial metal 3D printer was released by Electro Optical Systems (EOS), a German company. As technology has matured, 3D printing has grown quickly and become a viable manufacturing method for all types of industrial applications.

Additive manufacturing. Photo from Monroe Engineering.
Traditional Manufacturing
Subtractive manufacturing is likely the oldest method of creating a desired shape: take a “blank” part and remove material until you have the shape you need. The upside to this type of production is immense control over shapes for very accurate parts and a repeatable process. Over time, more efficient material removal methods have been created, but material is always removed, which can create a significant amount of waste. The tool that does the cutting also has to be able to reach all the areas of the part to shape them, which limits the geometry of some pats, especially internal pathways and lattice-type designs. Moving the part for the cutting tool to reach difficult areas also adds time and cost.
Formative manufacturing involves processes like injection molding or stamping that uses pressure and/or heat to create the desired shape. Operations like stamping can be done very quickly, but the cost to create molds and set up machines means a much high upfront cost that is only recouped by high volume. Luckily, after the fixed costs of setup, the variable costs are low compared to other forms of manufacturing. Formed parts are also usually simpler in design, and although molten metals can flow into a form, removing the part from a mold creates additional costs not present with stamping.

Milling process. Photo from CNCLathing.
So why do we need Additive Manufacturing? What are the applications?
AM works very well for low volume parts or where designs are changed frequently. It also works well for one-off parts, like the part for an old machine who’s maker is no longer in business. Printing does great for creating complex parts, as internal cavities and fluid pathways are just as easy to print as a solid block, and in fact use less material and take less time. The proliferation of additive manufacturing means some parts that were too expensive to produce or may not have even been possible with other manufacturing methods are now only limited by the designer’s imagination. Parts can also be created with a lattice structure to reduce weight and material, further lightening weight and lessening cost while keeping strength. Some downsides are that printed parts can be anisotropic, or not fully dense, meaning they may not be as strong as other methods like stamping and forging. Variations in cooling can also cause slight differences, meaning pieces may vary and not be identical batch to batch.
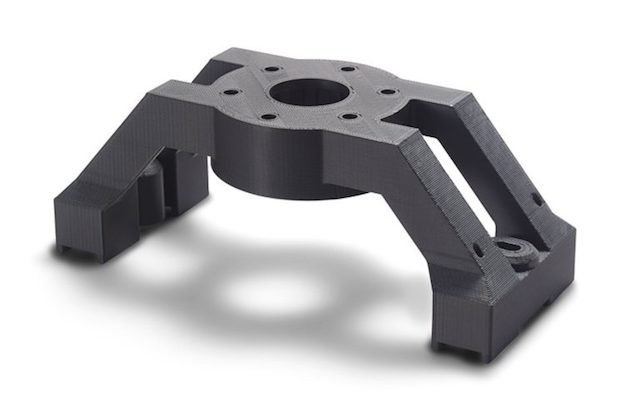
“New Diran 410MF07 nyIon-based materiaI for the F370 3D printer”. Image from TCT Magazine.
AM also means that if a facility is equipped with a printer, their only transportation cost is delivery of the printing material. For example, the traditional process for replacing a component in a machine is to order the part from the manufacturer, who either has it on the shelf or makes it, then ships it to the customer. With a printer, the part doesn’t have to be shipped, saving shipping costs, fuel, emissions, inventory costs and shipping time. This is one of the reasons wind turbine manufacturers are building facilities on the east coast of the United States – if they produce parts right on the shore, they don’t have to worry about the logistics of transporting a 100 meter long turbine blade across the country. The same is true for small and large parts alike.

Transporting an 88.4 meter turbine blade. Image from Mammoet.
There are 7 types of 3d printers, according to HUBS:
Vat photopolymerization: photopolymer resin is exposed to an ultraviolet laser beam, making it solid. This process creates smooth surfaces and good detail, but parts are brittle and UV sensitive.
Powder bed fusion: PBF uses heat to fuse plastic or metal particles a layer at a time. This creates strong parts of any geometry and size, but takes longer and costs more than other methods.
Material extrusion: material is squeezed through a nozzle in layers, the most common form of 3D printing. It’s fast, low cost, and uses common plastics, but can create rough, anisotropic finishes, isn’t scalable, and not as accurate as other print types.
Material jetting: UV light hardens materials like polymer, wax, or metal layer by layer. This method is high in detail and accuracy, including a smooth finish, but is costly and parts are brittle.
Binder jetting: uses a binding agent to adhere thin layers of powder without heat. It can produce all sorts of color in different materials and doesn’t warp because it doesn’t have to cool. The strength and accuracy of parts is lower than other methods like material jetting.
Direct energy deposition: DED melts powder to create objects, frequently used with metal wire or powder. It creates strong parts in lots of materials, but is high in cost and can have a poor finish.
Sheet lamination: laminates thin sheets of material creating a fast, low cost structure that may need finishing.
It’s fascinating how many types of 3D printing there are, especially photopolymerization, which looks like the parts are forming themselves out of a vat of goo. For commercial purposes, there are many options all dependent on the type of material and the goal of the part. Resolution is also important to consider and works just like computer resolution – the higher the resolution the smoother the transitions will be but the more time it will take as smaller areas are being printed with each pass. No matter the quality, essentially 3D printing is just building an object out of small slices of material one layer at a time.
Check out the video below of vat photopolymerization:
Video from Hubs YouTube channel.
Maritime and Offshore Applications
Kongsberg Ferrotech partnered with Equinor, SINTEF, and Gassco to work on underwater 3D printing tech for subsea repair and maintenance. The idea is to use an underwater robot to go to a damaged pipeline, cover it, and print the material to repair it in place – no need to pull the pipe up or send divers down.

Credit: Kongsberg Ferrotech. Image from Offshore Engineer.
GE Renewable Energy is testing 3D printed wind turbine blade tips. Printing these pieces will help reduce weight for better power generation and lower maintenance. Compared to standard glass or carbon fiber blades, the printed parts are also recyclable to close the loop on the material’s lifecycle.
3D printed parts are already being used on oceangoing vessels. ConocoPhillips Polar Tankers used parts from a partnership collaboration between ABS, Sembcorp, and 3D Metalforge on their tanker ships, including a gear set, nozzle, and a flexible coupling. ABS said the materials were of higher quality that traditional materials and the Navy has even started using hundreds of printed parts. ABS has also published guidelines on using printed parts. These types of small parts are also beneficial because drone delivery technology allows smaller parts to be delivered fast to offshore installations. Additive manufacturing facilities near the coast can now get parts to vessels and rigs offshore in a fraction of the time with the help of drones.
Huisman may be the most impressive of all as they 3D printed 350mt rated crane hooks weighing 1,700kg, made from 90 kilometers of welding wire. The process saves time compared to forging and casting components, and they have plans to make facility upgrades that will allow 5,000kg hooks to be produced.

Huisman 3D printed crane hook. Image from Offshore Engineer.
The Future of 3D Printing and Additive Manufacturing
Additive manufacturing is the complete opposite of traditional manufacturing – creating objects by adding to them, rather than removing material or forcing it into a mold. In the near future, it is predicted that additive manufacturing will help to decarbonize, reduce waste, save energy, and create lighter-weight plant-based materials. The biggest hurdle will be volume production, but AM will continue make strides due to other benefits like reduced transportation costs. The ability to customize products will also be a big driver, normally custom says expensive, but it may become the norm. Supply chain disruptions could become a concern of the past as companies produce their own parts – a supplier could even send the order to the customer’s printer for fulfillment, never touching a shipping container or box. Industry 5.0 is on the way with smart factories and additive manufacturing will be a big part of the facture of the future. The replicator from Star Trek may not be far off, where we request an item and it materializes in front of us, although maybe taking a bit longer than a couple of seconds.
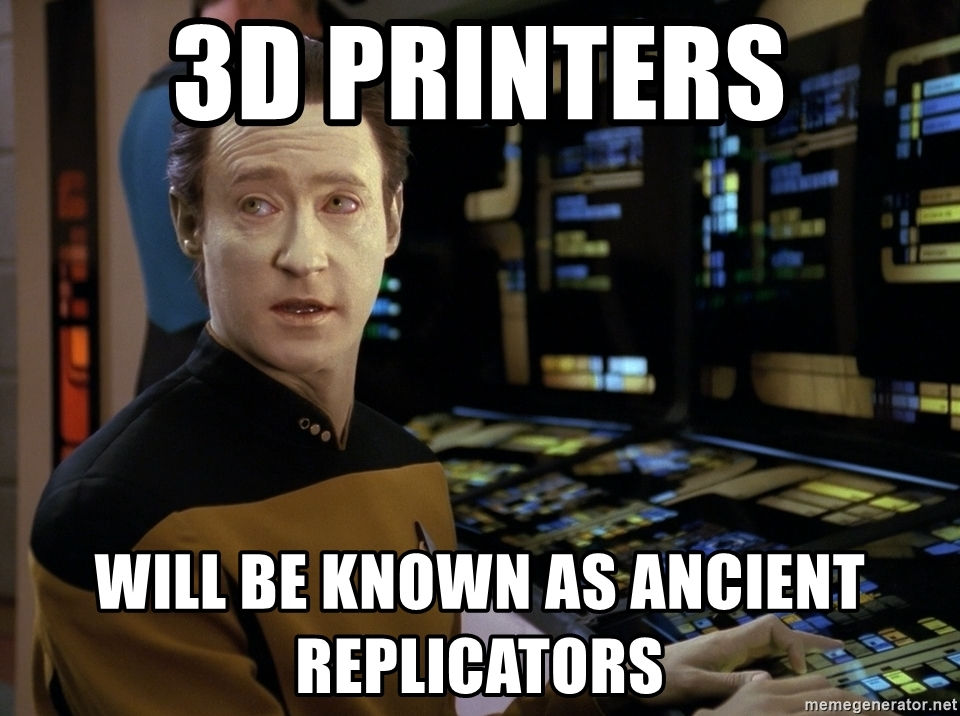
Image from Memegenerator.net.
Happy Friday!
PS – check out Hubs article on 3D printing, they have a ton of great information and videos!
Sources:
Comments